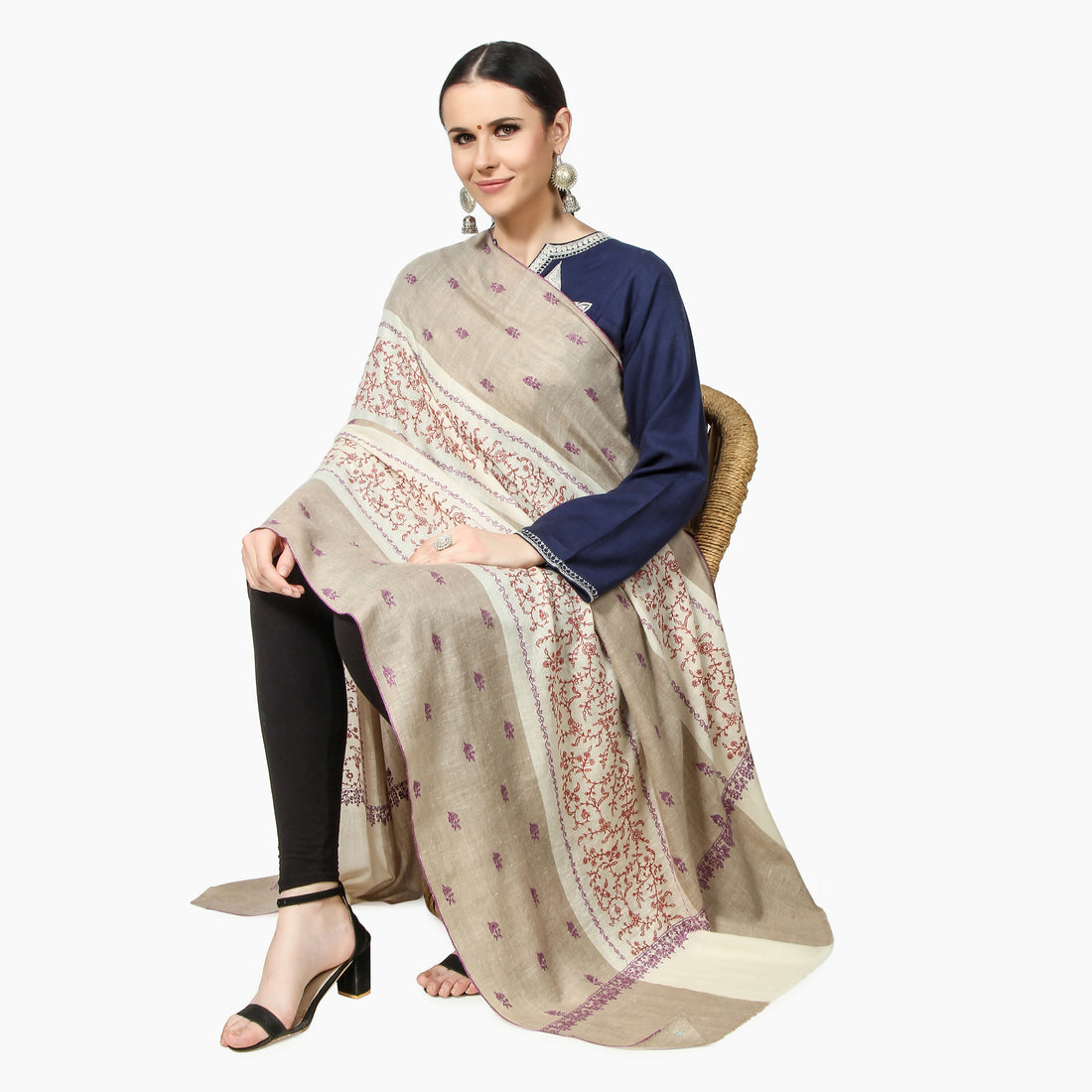
The Craftsmanship of Cashmere Pashmina
Share
Cashmere, known for its luxurious softness and warmth, has a rich history dating back centuries. Originating from the soft undercoat of cashmere goats, this prized fiber has been coveted for its rarity and quality. The term "cashmere" itself derives from the Kashmir region of India, where the fiber was first spun and woven into shawls and garments.
Pashmina, often referred to as "cashmere pashmina," specifically denotes the fine, lightweight wool derived from the underbelly of certain Himalayan goats, particularly those in the Changthangi region of Ladakh. The word "pashmina" is of Persian origin, meaning "soft gold," reflecting the preciousness of this textile.
Significance of Cashmere Pashmina in fashion and culture
Throughout history, cashmere pashmina has held a revered status in both fashion and culture. In ancient times, it was reserved for royalty and nobility due to its rarity and exceptional qualities. Its association with luxury and elegance has persisted through the ages, making it a symbol of sophistication and refinement.
In fashion, cashmere pashmina is renowned for its versatility and timeless appeal. It has adorned the shoulders of style icons, graced the runways of haute couture, and become a staple in the wardrobes of discerning individuals worldwide. Whether as a cozy scarf, an exquisite shawl, or a sumptuous sweater, cashmere pashmina elevates any ensemble with its unmatched softness and drape.
Beyond its sartorial allure, cashmere pashmina holds deep cultural significance in regions where it is produced. In Kashmir, for example, the art of weaving intricate pashmina shawls has been passed down through generations, representing not just a craft, but a way of life. These shawls are often treasured heirlooms, woven with stories of tradition and craftsmanship.
C. Overview of the craftsmanship involved
The creation of cashmere pashmina involves a meticulous process that combines age-old techniques with modern innovation. From the careful selection of raw fibers to the intricate weaving of the final product, every step requires skilled hands and a deep understanding of the material.
Craftsmen begin by combing the soft undercoat of cashmere goats, separating the fine fibers from the coarser outer layer. This painstaking task yields only a small quantity of usable cashmere, further underscoring its rarity and value.
Next, the raw cashmere is spun into yarn using traditional spinning wheels or modern machinery, depending on the desired outcome. The quality of the yarn is paramount, as it determines the texture, strength, and luster of the finished pashmina.
Weaving, whether done by hand on traditional looms or by automated machines, is where the magic truly happens. Skilled artisans meticulously interlace the yarn to create intricate patterns and designs, imbuing each piece with its own unique character. The weaving process requires precision and patience, as even the slightest imperfection can affect the final result.
Finally, the finished fabric undergoes careful finishing touches, such as washing, blocking, and pressing, to enhance its softness and drape. Each piece is inspected for quality and craftsmanship before being ready for sale, ensuring that only the finest cashmere pashmina reaches the hands of discerning customers.
The Origin of Cashmere
A. Geographic origins of Cashmere
Cashmere, often referred to as "soft gold," originates from the rugged landscapes of Central and East Asia. The primary regions known for cashmere production include Kashmir, Mongolia, China, Iran, Afghanistan, and India. However, it is the remote mountainous terrain of the Kashmir region in northern India and Pakistan that holds a special place in the history of cashmere.
For centuries, the harsh winters and high altitudes of Kashmir have provided the ideal conditions for cashmere goats to thrive. The extreme cold prompts these goats to grow a soft, insulating undercoat to protect themselves from the elements. It is this fine undercoat that is harvested and spun into the luxurious fiber known as cashmere.
B. How Cashmere is sourced from goats
The process of sourcing cashmere begins with the careful combing or shearing of the goats during the spring molting season. Unlike sheep, which are typically shorn annually, cashmere goats shed their winter coats naturally, making the collection of cashmere fibers a labor-intensive task.
Traditionally, skilled herders use special combs or brushes to gently separate the soft undercoat from the coarser outer hair of the goats. This delicate task requires patience and precision to ensure that only the finest cashmere fibers are collected.
In some regions, particularly in Mongolia and China, herders may also employ shearing techniques to gather cashmere fibers. However, this method is less common and requires careful handling to avoid damaging the delicate fibers.
Once harvested, the raw cashmere is sorted and graded based on its quality, fineness, and color. The finest and longest fibers are highly prized for their superior softness and warmth, commanding premium prices in the global market.
C. Characteristics of Cashmere fiber
Cashmere fiber is renowned for its exceptional qualities, which set it apart from other types of wool. Unlike traditional sheep's wool, which can be coarse and prickly, cashmere is incredibly soft and luxurious to the touch.
The unique structure of cashmere fibers contributes to its remarkable insulating properties, making it exceptionally warm yet lightweight. This natural warmth, combined with its breathability, allows cashmere garments to regulate body temperature in varying climates, ensuring comfort and coziness year-round.
In addition to its softness and warmth, cashmere is also prized for its durability and resilience. Despite its delicate appearance, cashmere fibers are surprisingly strong and resistant to pilling, ensuring that garments retain their smooth texture and appearance over time.
Furthermore, cashmere has a distinctive luster and drape that lends an air of elegance to any garment. Its ability to absorb and retain dyes also allows for a wide range of vibrant colors and rich hues, enhancing its appeal in the world of fashion and design.
The Art of Spinning
A. Traditional spinning techniques
Spinning cashmere into yarn is an ancient craft that requires skill, patience, and precision. Traditionally, this process was performed by hand using simple tools such as drop spindles or spinning wheels. Skilled artisans would carefully draft and twist the delicate cashmere fibers into fine threads, creating yarn of varying thickness and texture.
In regions like Kashmir, where the art of spinning has been practiced for centuries, traditional techniques have been passed down through generations. The rhythmic motion of the spinner's hands, coupled with their intimate knowledge of the fiber, results in yarn that is both uniform and resilient.
B. Modern innovations in spinning
While traditional spinning techniques remain prevalent in some regions, modern innovations have revolutionized the process of spinning cashmere. Industrial spinning machines can produce yarn at a much faster rate and with greater consistency than is possible by hand.
These machines are equipped with advanced mechanisms that precisely control the drafting and twisting of the fibers, resulting in yarn of uniform thickness and quality. While some purists may argue that hand-spun yarn retains a certain charm and character, the efficiency and scalability of modern spinning machines have allowed cashmere production to meet the demands of a global market.
C. Importance of yarn quality in Cashmere Pashmina
Regardless of the spinning method employed, the quality of the yarn plays a crucial role in the production of cashmere pashmina. Fine, well-spun yarn enhances the softness, drape, and durability of the final product, ensuring that it meets the exacting standards of discerning customers.
High-quality yarn also allows for greater versatility in design and weaving, enabling artisans to create intricate patterns and textures with ease. Additionally, yarn that is free from imperfections such as knots or irregularities ensures a smooth and luxurious finish, enhancing the overall aesthetic appeal of cashmere pashmina garments and accessories.
Weaving and Looming
A. Traditional hand-weaving methods
In the art of weaving cashmere pashmina, traditional hand-weaving methods have long been revered for their precision and artistry. Skilled artisans work on hand looms, meticulously interlacing the yarn to create intricate patterns and designs.
Each pass of the shuttle, each movement of the weaver's hands, is a testament to the centuries-old tradition of craftsmanship that defines Kashmiri weaving. From simple stripes to complex paisley motifs, every pattern is executed with care and attention to detail, resulting in textiles of unparalleled beauty and quality.
B. Introduction of mechanized looming
In recent decades, mechanized looming has become increasingly common in cashmere pashmina production, particularly in larger-scale operations. These automated looms are capable of weaving fabrics at a much faster rate than traditional hand looms, making them well-suited to meet the demands of a global market.
While mechanized looming offers greater efficiency and consistency, some purists argue that it lacks the human touch and artistry of traditional hand weaving. However, advancements in technology have allowed for greater customization and control, enabling artisans to create complex designs with precision and accuracy.
C. Impact of weaving techniques on the final product
The weaving technique employed has a significant impact on the final appearance and quality of cashmere pashmina. Whether hand-woven or machine-woven, the choice of weave pattern, density, and tension can influence factors such as drape, texture, and durability.
Traditional hand-woven cashmere pashmina often boasts a slightly irregular texture and a luxurious drape that is difficult to replicate with mechanized looming. On the other hand, machine-woven fabrics may offer greater consistency and uniformity, making them ideal for mass production.
Dyeing and Coloration
A. Natural dyeing processes
The allure of natural dyes lies in their rich hues and eco-friendly properties, making them a preferred choice for many artisans crafting cashmere pashmina. Natural dyes are derived from plant sources such as roots, leaves, bark, and flowers, as well as from animal and mineral sources.
Artisans skilled in the art of natural dyeing carefully extract pigments from these organic materials through processes such as boiling, fermenting, or soaking. Each dye material imparts its own unique color palette, ranging from earthy tones like indigo and madder to vibrant hues like saffron and cochineal.
The use of natural dyes not only enhances the aesthetic appeal of cashmere pashmina but also contributes to sustainable and environmentally conscious production practices.
B. Synthetic dyeing methods
In addition to natural dyes, synthetic dyes offer a wide range of colors and shades that may be difficult to achieve with natural materials alone. Synthetic dyes are chemically synthesized compounds that provide vibrant, long-lasting colorfastness to cashmere pashmina.
The process of synthetic dyeing involves dissolving the dye molecules in a solvent and then immersing the cashmere fibers in the dye bath. Through precise control of temperature, pH, and dye concentration, artisans can achieve uniform and consistent coloration across the fabric.
While synthetic dyes offer versatility and reliability, concerns have been raised about their environmental impact and potential health hazards. As a result, many producers are exploring alternative dyeing methods that prioritize sustainability and safety without compromising on color quality.
C. Significance of color choices in cashmere pashmina
The choice of colors in cashmere pashmina plays a significant role in defining its aesthetic appeal and marketability. From timeless neutrals like ivory and charcoal to bold statement shades like crimson and emerald, color selection reflects trends, cultural influences, and individual preferences.
In fashion, color can evoke emotion, convey personality, and make a powerful style statement. Soft pastels exude femininity and elegance, while jewel tones exude opulence and luxury. Additionally, cultural symbolism and traditions may dictate certain color preferences, with hues like red symbolizing prosperity and good fortune in many Asian cultures.
Ultimately, the significance of color choices in cashmere pashmina lies in their ability to enhance the beauty and versatility of the fabric, allowing wearers to express their unique sense of style and personality.
Embroidery and Embellishments
A. Traditional embroidery styles
Embroidery has long been synonymous with luxury and craftsmanship in the world of cashmere pashmina. Traditional embroidery styles, rooted in centuries-old techniques, showcase intricate patterns and motifs that are emblematic of the artisan's skill and creativity.
In regions like Kashmir, where embroidery has been practiced for generations, artisans employ techniques such as Kashmiri, Aari, and Sozni embroidery to embellish cashmere pashmina with exquisite detail. These styles often feature delicate threadwork, intricate motifs inspired by nature, and meticulous attention to stitch density and tension.
B. Contemporary embellishment techniques
While traditional embroidery styles continue to be cherished, contemporary embellishment techniques offer a fresh perspective on cashmere pashmina design. Modern artisans experiment with innovative materials, such as sequins, beads, and metallic threads, to create bold and eye-catching embellishments that appeal to contemporary tastes.
Embroidery may be combined with other embellishment techniques, such as appliqué, patchwork, and hand-painting, to create dynamic and multidimensional designs. These contemporary embellishments add a touch of modernity and sophistication to traditional cashmere pashmina, appealing to a diverse range of consumers.
C. Role of embroidery in enhancing the beauty of cashmere pashmina
Embroidery plays a pivotal role in enhancing the beauty and value of cashmere pashmina, transforming simple fabrics into works of art. Whether employing traditional or contemporary techniques, skilled artisans infuse each piece with a sense of artistry and craftsmanship that elevates it beyond mere clothing to a coveted accessory or heirloom.
Embroidery adds texture, depth, and visual interest to cashmere pashmina, creating a tactile and sensory experience for the wearer. Whether adorning a scarf, shawl, or sweater, embroidered motifs tell a story of culture, tradition, and heritage, making each piece a timeless treasure to be cherished for generations.
Quality Control and Finishing
A. Inspection processes to ensure quality
Quality control is a critical aspect of cashmere pashmina production, ensuring that every piece meets the highest standards of craftsmanship and durability. Throughout the production process, artisans conduct rigorous inspections to identify and rectify any defects or inconsistencies in the fabric.
From the selection of raw materials to the final finishing touches, each stage of production undergoes thorough scrutiny to ensure that only the finest quality cashmere pashmina reaches the hands of consumers. Inspections may include checks for fiber fineness, yarn strength, color consistency, and weaving precision, among other criteria.
B. Finishing touches to enhance durability and softness
Once the fabric has been woven, it undergoes a series of finishing touches to enhance its durability, softness, and overall aesthetic appeal. Finishing processes may include washing, blocking, brushing, and steaming, each designed to refine the texture and drape of the fabric.
Washing removes excess oils, dirt, and impurities from the fibers, resulting in a softer and more supple feel. Blocking ensures that the fabric maintains its shape and dimensions, while brushing or raising the nap enhances its warmth and plushness. Steaming helps to relax the fibers and remove any wrinkles or creases, leaving the fabric smooth and lustrous.
C. Packaging and presentation of the final product
The packaging and presentation of cashmere pashmina are as important as the product itself, reflecting the brand's commitment to quality, luxury, and attention to detail. Each piece is carefully folded, wrapped, and packaged in a manner that preserves its pristine condition and enhances its visual appeal.
Luxurious materials such as tissue paper, silk ribbons, and branded boxes are often used to package cashmere pashmina, adding to the sense of elegance and sophistication. Additionally, informative labels and care instructions ensure that customers can enjoy their purchase for years to come, maintaining its beauty and longevity.
Sustainability and Ethical Practices
A. Environmental impact of cashmere production
While cashmere pashmina is celebrated for its unparalleled softness and warmth, its production can have significant environmental consequences. Cashmere goats graze in delicate ecosystems, often leading to overgrazing and soil degradation. This can result in desertification and habitat loss, threatening the biodiversity of the region.
Moreover, the processing of cashmere fibers involves chemical treatments and dyes, which can pollute waterways and harm local ecosystems. Additionally, the energy-intensive nature of spinning and weaving contributes to greenhouse gas emissions and climate change.
B. Fair trade practices in the cashmere industry
Recognizing the social and economic challenges faced by cashmere-producing communities, many brands have embraced fair trade practices to ensure that workers receive fair wages and safe working conditions. Fair trade certifications guarantee transparency and accountability throughout the supply chain, empowering artisans and herders to earn a living wage and improve their livelihoods.
Fair trade initiatives also prioritize community development projects, such as education, healthcare, and infrastructure improvements, to foster sustainable growth and prosperity in cashmere-producing regions.
C. Efforts towards sustainability and ethical sourcing
In response to growing concerns about the environmental and social impacts of cashmere production, industry stakeholders are increasingly embracing sustainability and ethical sourcing practices. This includes initiatives to promote responsible grazing management, reduce water and energy consumption, and minimize waste and pollution throughout the production process.
Furthermore, efforts are underway to promote the use of organic and natural dyes, as well as to explore alternative fiber sources that are less resource-intensive and environmentally damaging. Brands are also partnering with local cooperatives and non-profit organizations to support conservation efforts and empower communities to protect their natural resources.
Conclusion
A. Recap of the craftsmanship involved in cashmere pashmina production
The production of cashmere pashmina is a labor-intensive process that involves skilled artisans and centuries-old techniques. From the careful combing of cashmere goats to the meticulous weaving of intricate patterns, each step requires precision, patience, and artistry.
B. Appreciation of the cultural and fashion significance
Beyond its technical prowess, cashmere pashmina holds deep cultural and fashion significance. Woven into the fabric of history, it has adorned royalty and captivated fashionistas with its timeless elegance and luxury. Its intricate patterns and vibrant colors tell stories of tradition and craftsmanship, making it a cherished accessory for generations.
C. Call to support sustainable and ethical practices in the industry
As consumers, we have the power to drive positive change in the cashmere industry by supporting brands that prioritize sustainability and ethical sourcing. By choosing products that are produced with care for the environment and respect for workers' rights, we can ensure that the legacy of cashmere pashmina endures for future generations to enjoy.
Together, let us embrace a future where luxury and sustainability go hand in hand, where craftsmanship and conscience converge to create a more equitable and environmentally conscious world.